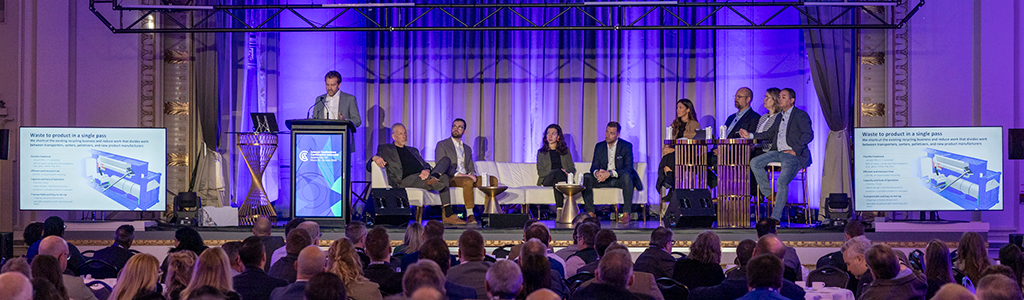
Resolve Plastics voted most exciting innovation at CCA’s 2025 Annual Conference
Our planet is choking on plastic.
Davin MacIntosh, Resolve Plastics
According to the Organization for Economic Co-operation and Development’s (OECD) first Global Plastics Outlook, plastic waste has more than doubled since the year 2000. At the heart of this global crisis, Resolve Plastics is leading the charge toward a cleaner, more sustainable future. The company’s vision is to create a world where plastic waste is not only diverted or removed from the environment but also repurposed to drive both economic and social progress for generations to come.
Davin MacIntosh, CEO of Resolve Plastics, was one of five innovators selected to showcase their groundbreaking solution during the Innovators’ Pitch: CONtact mentorship session at the 2025 CCA Annual Conference in Quebec City.
The CONtact Mentorship program, presented in partnership with the National Research Council of Canada’s Industrial Research Assistance Program, offers small and medium enterprises the chance to share their innovations with the industry. Through meetings with industry representatives, the program helps entrepreneurs refine their product or service for industry adoption. The experience culminates with a high-profile presentation to over 500 delegates at the Annual Conference.
Following the presentations, delegates voted for the innovation they found most compelling – and Resolve Plastics emerged as the winner, hailed for their visionary approach to tackling plastic waste.
Catch Davin’s winning presentation below.
CCA caught up with Davin after the conference to discuss his innovation, as well as his experience with the CONtact mentorship program.
CCA: How did Resolve Plastics come to be? Why this particular innovation?
As an entrepreneur with a background in environmental law, I believe that the world will face a reckoning in dealing with the exponentially increasing volume of plastic waste. I have travelled extensively and witnessed first-hand the problem of plastics entering the environment and oceans. It’s such a pernicious problem because plastic doesn’t break down like organics. North America only recycles 9 per cent of plastic waste, but the problem is hidden because most of it is incinerated or hidden in landfills. What many people don’t realize is that plastic makes up about a third of the volume of material entering landfills, and that comes at a cost.
To solve the problem, the world needs practical, economic solutions. Yet – after years of studying available recycling technologies – I saw almost no cost-effective ones. Then I found an inventor who had been working on a relatively simple and inexpensive process to turn waste plastic into blocks and was intrigued. After a year of R&D we started Resolve Plastics and have been working to make the process viable at commercial scale.
The RPMachine will convert up to three tonnes per hour of unsorted, mixed plastic waste into R-Blocks. The RPMachine is the size of a sea-can or semi trailer and can be set up anywhere with power and water. The magic is its relative simplicity – it’s a robust machine that uses a mechanical process.
The RPMachine shortcuts the recycling process. Most recycling programs involve several companies and facilities: one to collect, one to sort, one to pelletize, and one to make new products. In comparison, the RPMachine takes all plastic and produces a valuable building material (R-Blocks) in a single pass. Transpiration costs (both for waste plastic and for blocks) are significantly reduced, because RPMachines can be set up locally.
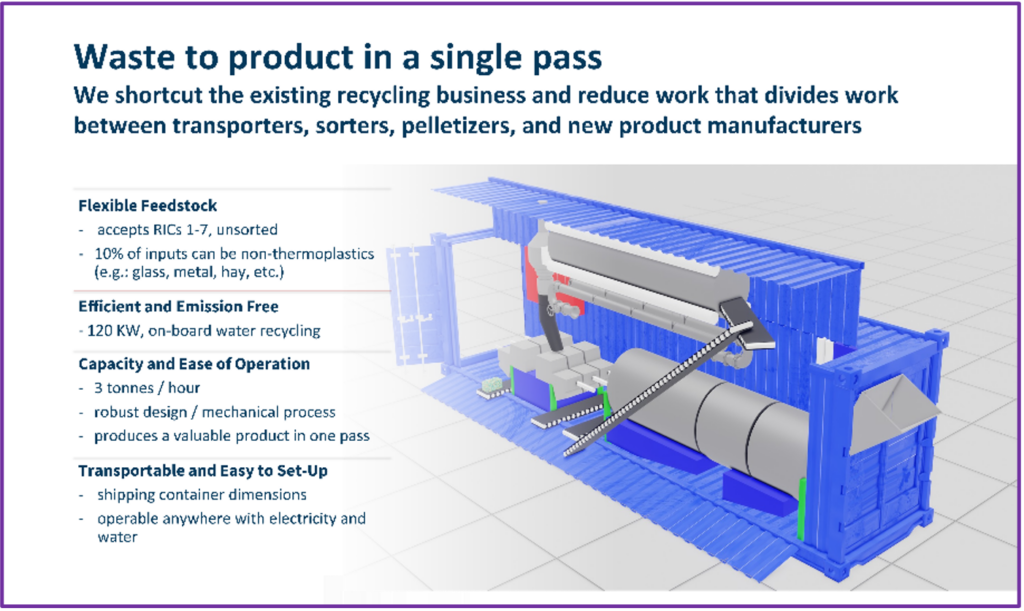
CCA: How has your participation in CONtact and pitching your solution at the conference helped you? Was there any advice or question that stood out, and how will it influence your future work?
It was a privilege to attend the CCA conference in Quebec City. It was a great opportunity to network with leaders in Canada’s construction industry. One thing that really impressed me was how many people I met who had built companies from the ground up – people who aren’t afraid to work hard to solve practical problems.
For the last couple of years, we have been focused on the value proposition to the recycling industry and on technology development. The CCA conference opened our eyes to the interests of the construction sector and the vast range of potential applications for R-Blocks. In just a few short conversations I was introduced to several potential applications that we hadn’t even thought of! We have already significantly expanded our network and are discussing potential partnerships now and in the future.
CCA: Can you highlight three key aspects of Resolve Plastics that would resonate with the institutional, commercial, industrial, civil and multi-residential construction sector about Resolve Plastics?
I believe that Resolve Plastics has the potential to play a significant part in the global waste problem by creating a versatile and extremely inexpensive construction material. R-Blocks could replace concrete and cinder blocks in many applications, for a fraction of the cost, and with major environmental benefits.
- For roughly the same cost as landfilling plastic, we can turn it into R-Blocks.
- R-Blocks are durable, insulative, and easy to transport and handle.
- The environmental and carbon related benefits of using R-Blocks will unlock opportunities for the construction industry.
CCA: What has been the biggest challenge for you so far, and your biggest success?
Despite the gravity of the problem and the exponential increase in plastics production, it has been a challenge to raise awareness and find partners ready to lead innovation. The Covid years led to a significant surge in the use of plastic products, including PPE and food storage. While this makes sense, it came with a decreased focus on the challenges of dealing with post-consumer plastic.
More recently, we have benefited from significant investment from government granting agencies and a few angel investors. This has allowed us to make great progress on the design and testing of our new process.
CCA: What are the next steps for your company?
Resolve Plastics is just wrapping up a project to pilot the new components and register new IP. This new process will increase processing capacity by more than 10X. We are working on the final design for the full-scale RPMachine. The next step will be to fabricate the new RPMachine and demonstrate it in a commercial application.
CCA: For those firms that may be interested in becoming a technology acceleration partner, what are you looking for, and how do they connect with you?
At this point we are looking for a partner in the demonstration of our new RPMachine design at full scale. This partner would contribute a portion of the cost of setting up the first machine and operating it during a test phase. They will benefit from decreased plastic disposal costs, access to R-Blocks, equity in the company, and lots of media and PR opportunities. The project is getting increasing attention and is a great opportunity to demonstrate leadership and support for an innovation that can benefit humanity.
For more information, videos, and to contact Resolve Plastics, please visit resolveplastics.com.
Become a CONtact mentor or mentee – Next round opens this summer!
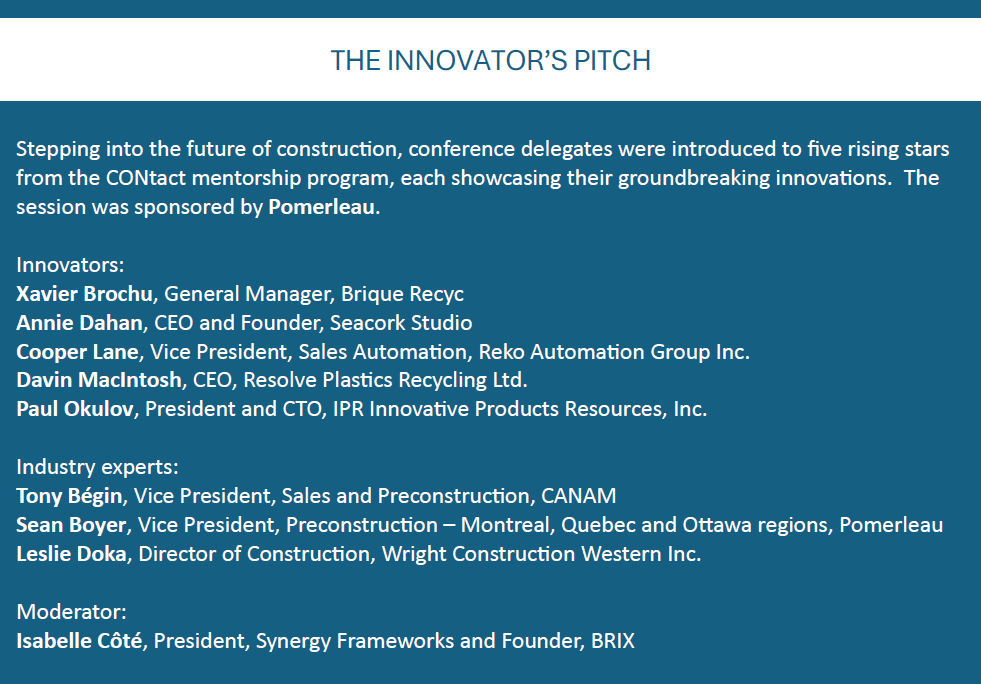